Common Challenges in Manufacturing Workflow Management and How to Overcome Them
- susanobrienfin
- Feb 18
- 3 min read
Manufacturing workflow management is essential to ensure the smooth operation of production processes, reduce delays, and maximize efficiency. However, businesses face several challenges that can hinder optimal performance. In this blog, we will explore the most common obstacles in manufacturing workflow management and provide actionable strategies to overcome them.
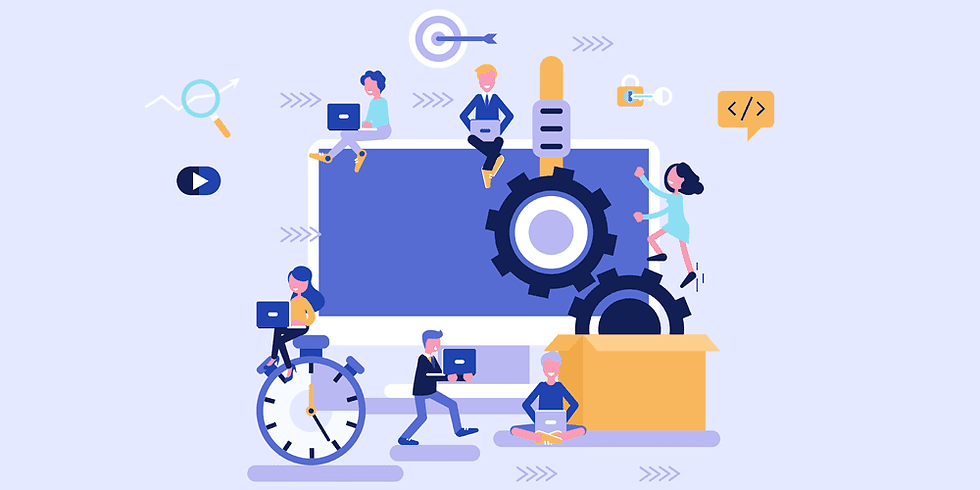
1. Inefficient Communication Between Departments
Challenge: One of the most prevalent challenges in manufacturing workflow management is poor communication between different departments, such as production, inventory, and quality control. Miscommunication can lead to mistakes, delays, and a lack of coordination, which ultimately affects the production schedule.
Solution: Implementing an integrated communication system is crucial. Using cloud-based platforms that allow real-time updates and collaboration between departments can significantly improve communication. This ensures that everyone is on the same page regarding orders, deadlines, and priorities.
2. Lack of Visibility into the Workflow
Challenge: Without proper visibility into the workflow, manufacturers often struggle to track the progress of production processes, identify bottlenecks, or foresee potential issues. This lack of transparency can result in delays, excessive downtime, or missed deadlines.
Solution: Adopting digital tools like Manufacturing Execution Systems (MES) or Enterprise Resource Planning (ERP) software can provide comprehensive visibility into workflows. These systems track every stage of production, from raw material procurement to final assembly, giving managers the ability to spot inefficiencies and make adjustments in real time.
3. Inventory Management Issues
Challenge: Maintaining the right balance between supply and demand is a significant hurdle for manufacturers. Overstocking can tie up capital, while understocking can lead to production delays. Ineffective inventory management can also result in production stoppages, backorders, and customer dissatisfaction.
Solution: Implementing a just-in-time (JIT) inventory system can help streamline inventory management. By synchronizing material procurement with production schedules, manufacturers can reduce inventory costs and minimize the risk of stockouts. Additionally, using automated inventory tracking systems allows for real-time updates on stock levels, helping to avoid human error.
4. Quality Control Challenges
Challenge: Maintaining consistent product quality is critical in manufacturing, but quality control can be challenging when there are variations in raw materials, machinery, or human error. Failure to meet quality standards not only results in increased costs due to rework or scrap but also damages a company's reputation.
Solution: Introducing automated quality control processes, such as sensor-based inspection systems or machine vision technology, can significantly improve consistency and accuracy. These technologies can detect defects early, reducing the chances of faulty products reaching the final stages of production. Regular employee training and process standardization also play a key role in ensuring high-quality output.
5. Process Bottlenecks
Challenge: Bottlenecks in manufacturing are a significant hurdle to productivity. A bottleneck occurs when a particular stage of production becomes overloaded, slowing down the entire process. This can be caused by outdated equipment, insufficient manpower, or inefficient workflows.
Solution: Identifying and eliminating bottlenecks should be a priority in workflow management. Conducting regular process audits and using data analytics tools to analyze performance can help pinpoint areas where bottlenecks occur. Investing in automation and upgrading equipment can also alleviate pressure on congested stages of production.
6. Inadequate Resource Allocation
Challenge: Resource allocation, including labor, machinery, and materials, is another critical challenge. Improper allocation can lead to production delays, excessive overtime, and overuse of machinery, which increases maintenance costs and reduces equipment lifespan.
Solution: By using advanced scheduling software, manufacturers can optimize resource allocation. These systems allow managers to align labor shifts, machine usage, and material procurement with the production schedule, reducing downtime and ensuring optimal use of resources.
7. Resistance to Change
Challenge: Manufacturing teams can often resist changes, especially when it comes to implementing new technologies or processes. This resistance can delay the adoption of more efficient workflows, stifling productivity and growth.
Solution: Overcoming resistance requires a change management strategy. Involve key stakeholders in decision-making, provide adequate training, and clearly communicate the benefits of adopting new workflows. Gradually introducing changes and offering support during the transition period can help ease the process.
Conclusion
Manufacturing workflow management can be complex, but by addressing these common challenges with the right strategies and tools, manufacturers can significantly improve efficiency, reduce costs, and increase product quality. By adopting integrated communication systems, enhancing visibility, implementing JIT inventory practices, automating quality control, eliminating bottlenecks, optimizing resource allocation, and managing change effectively, manufacturers can ensure a smoother, more productive operation.
SITES WE SUPPORT
SOCIAL LINKS
Comments